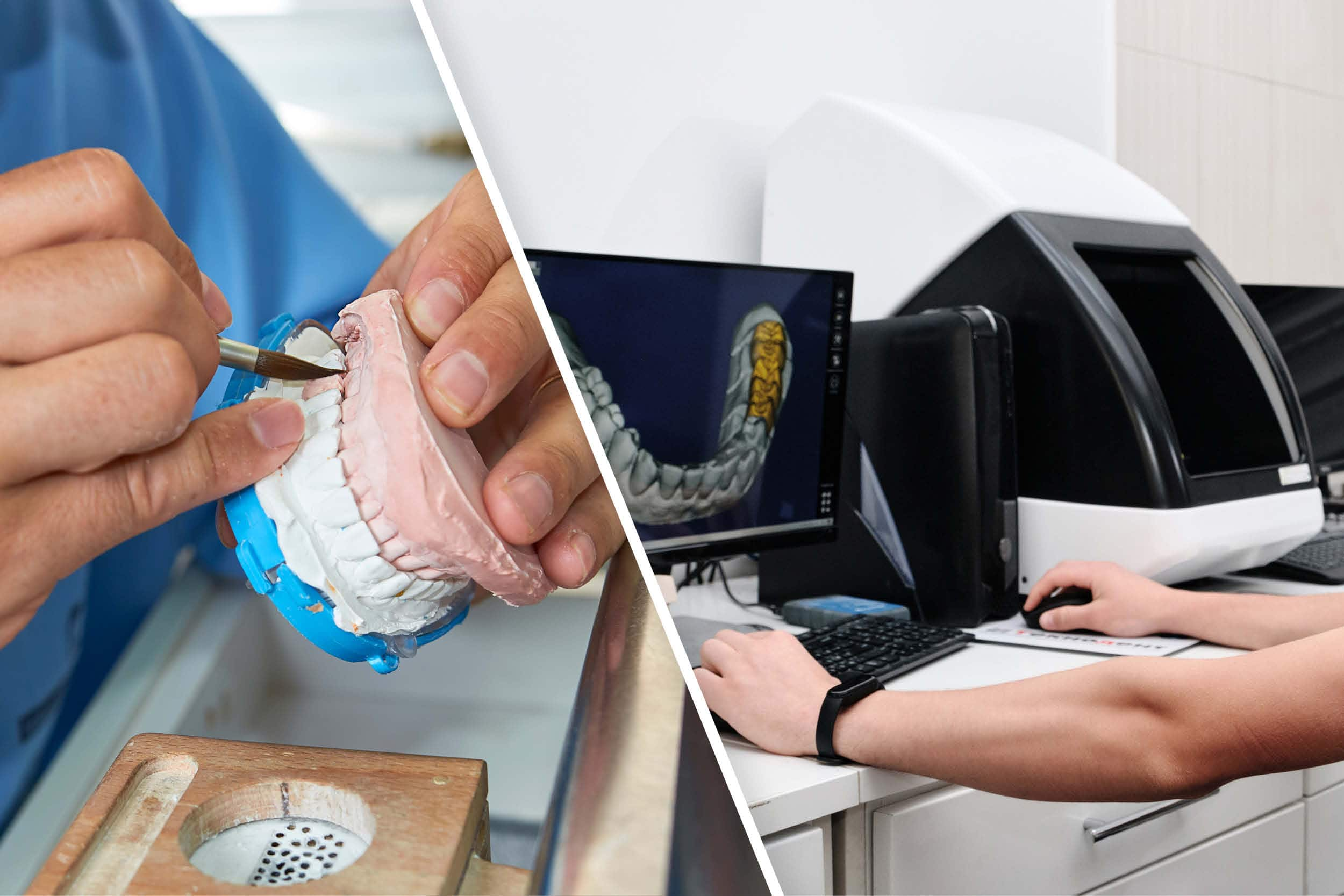
Dental laboratory technology is the main auxiliary trade for the dental profession and it supports dentistry both materially and technically. It is, by definition, the art and the science of fabricating devices to correct and/or replace natural teeth [1].
Dental laboratories are primarily concerned with the production of five categories of device [2]:
- partial or full fixed prostheses supported by natural teeth;
- full and partial removable prostheses;
- fixed, removable and maxillofacial prostheses supported by implants;
- orthodontic appliances, devices for sleep apnoea and mouth guards;
- maxillofacial prostheses such as ocular and craniofacial obturators.
However, dental technicians also provide other important services that facilitate the work of dentists, such as the fabrication of surgical templates for guided surgery, radiographic templates, and simple and complex temporary restorations [3].
All these operations are always based on the written instructions of dentists, who are the designers, as well as the supervisors, of prosthetic projects.
From manual art to industrial mechanics
Until a few years ago, these processes were carried out exclusively by means of direct and indirect sculpting techniques, such as lost-wax casting, model-making by adding or removing material (e.g. wax, ceramic firing, resin pressing, etc.).
Dental laboratory technology was therefore a predominantly manual art, which involved the use of instruments or equipment pertaining specifically to the field of craftsmanship.
Today, however, the situation has changed radically to favour technologies more akin to those of industrial mechanics. As a matter of fact, the current innovations in the field of dentistry include what we might call “the digital revolution of the dental laboratory” [4].
The introduction of digital systems has revolutionised workflows not only in dental practices, but also in dental laboratories [5,6].
The digital revolution of dental laboratories
Let’s take a closer look at the impact of the digital revolution on the workflows and the main technologies used by dental technicians.
Working times and production processes
In dental laboratories even more than in practices, workflows have been accelerated and processing times have been cut considerably, while simultaneously enhancing the mechanical properties of the materials used and introducing new ones [7,8].
Nevertheless, it is true that these systems still do not make it possible to make restorations with the same aesthetic properties (translucency, grading of different shades within the same structure) on a par with those of restorations fabricated manually by a technician.
Furthermore, in some cases, 3D model printing is a lengthy process, depending on the type of printer and the print parameters set (tilt of the model in relation to the work platform).
CAD/CAM systems consist of a scanner, software that processes the scan data and makes it possible to design the restorations, and a fabrication system that transforms the digital file into a physical restoration [9].
Want to find out more?
Discover the silicones and gypsums that are compatible with digital CAD/CAM systems
Zhermack offers a vast range of materials designed to ensure maximum performance in the acquisition of 3D data that can be scanned and read by the most common laser or optical scanners without using anti-reflective sprays.
Subtractive and additive techniques
The processes used to fabricate digital devices can be either subtractive or additive [10–12].
Subtractive production techniques involve obtaining the restoration, using a milling machine, starting from a block of industrially assembled material in the form of a disk or block [13,14].
Additive techniques, on the other hand, consist of the various 3D printing technologies [15,16]. Today’s digital dental laboratories use the abovementioned production methods for materials such as wax, resins, ceramics and hybrid ceramics [4,9].
Selective Laser Melting and Selective Laser Sintering
For harder materials, such as metals, production is often assigned to industrial milling and printing centres, which have higher performance milling machines and 3D printing technologies such as selective laser melting or selective laser sintering, which currently have costs that are prohibitive for a dental laboratory [17].
In both cases, however, the products of printing and milling are semi-finished devices that must necessarily be finished by a dental technician before they can be handed over to the clinician.
Depending on the material used, after milling a sintering step may be required in order to give the material the appropriate final shape and mechanical characteristics [18].
The post-processing of 3D printing
All 3D printing requires various post-processing procedures, which can also have an adverse effect on the final result unless they are carried out with due care [16].
In addition, certain analogue steps, such as the application of aesthetic finishes (pigments, glaze) or porcelain layering are still essential and therefore must be carried out manually by a dental technician [4].
The impact of new workflows on the dental technician profession
However, all these new workflows are taking their toll on the dental technician profession, where, in recent years, there has been not only a decrease in the number of professionals, but also a deterioration in the skills and knowledge that are fundamental for producing high-quality restorations [19].
As these workflows are a novelty, the lack of training provided to dental technicians regarding these digital techniques and the limited interaction with dentists during training programmes pose a severe threat to the entire patient care team, as future laboratory and clinical standards will be increasingly defined by commercial and industrial interests [2,19].
Furthermore, the new digital dental technicians often lack analogue knowledge, a heritage that is essential for ensuring high-quality work [20].
Are we headed for a deterioration in the creative aspect?
The issue should be dealt with from a deeper and more cultural perspective.
Once upon a time, a craftsman was considered someone who created and produced a product with a specific function with his or her own hands [21]. The prerequisite for his/her creation was the freedom with which he/she interacted with the stimulus for conception and the inspiration he/she received from the outside world to obtain a product that expressed his/her personal interpretation.
A craftsman therefore created, through his/her careful and precise work, unique and unreproducible objects [22]. On the contrary, industrialisation and mass mechanical production starting from a standard design or shape, to be subsequently adapted to the clinical case, eliminate that creative aspect, of attention and experimentation of any possible innovation that starts from scratch.
The question therefore remains whether new production technologies are culturally impoverishing not only the dental technician profession but also all artisanal and manufacturing professions where original, individual and genuine creation was once an added value.
References
[1] Chi è l’Odontotecnico – Informazioni – Antlo n.d. https://www.antlo.it/Informazioni/ChiELOdontotecnico (accessed March 18, 2023).
[2] Bobich AM, Mitchell BL. Transforming Dental Technology Education: Skills, Knowledge, and Curricular Reform. Journal of Dental Education 2017;81:eS59–64. https://doi.org/10.21815/JDE.017.035.
[3] Beretta M, Poli PP, Maiorana C. Accuracy of computer-aided template-guided oral implant placement: a prospective clinical study. J Periodontal Implant Sci 2014;44:184. https://doi.org/10.5051/jpis.2014.44.4.184.
[4] Masri R, Driscoll C. Odontoiatria digitale: Presupposti teorici e applicazioni cliniche. Edra; 2017.
[5] Maragliano-Muniz P, Kukucka ED. Incorporating Digital Dentures into Clinical Practice: Flexible Workflows and Improved Clinical Outcomes. J Prosthodont 2021;30:125–32. https://doi.org/10.1111/jopr.13277.
[6] Seelbach P, Brueckel C, Wöstmann B. Accuracy of digital and conventional impression techniques and workflow. Clin Oral Investig 2013;17:1759–64. https://doi.org/10.1007/s00784-012-0864-4.
[7] Alghazzawi TF. Advancements in CAD/CAM technology: Options for practical implementation. Journal of Prosthodontic Research 2016;60:72–84. https://doi.org/10.1016/j.jpor.2016.01.003.
[8] Grande F, Mochi Zamperoli E, Pozzan MC, Tesini F, Catapano S. Qualitative Evaluation of the Effects of Professional Oral Hygiene Instruments on Prosthetic Ceramic Surfaces. Materials 2021;15:21. https://doi.org/10.3390/ma15010021.
[9] Sulaiman TA. Materials in digital dentistry-A review. J Esthet Restor Dent 2020;32:171–81. https://doi.org/10.1111/jerd.12566.
[10] Auškalnis L, Akulauskas M, Jegelevičius D, Simonaitis T, Rutkūnas V. Error propagation from intraoral scanning to additive manufacturing of complete-arch dentate models: An in vitro study. Journal of Dentistry 2022;121:104136. https://doi.org/10.1016/j.jdent.2022.104136.
[11] Grande F, Tesini F, Pozzan MC, Zamperoli EM, Carossa M, Catapano S. Comparison of the Accuracy between Denture Bases Produced by Subtractive and Additive Manufacturing Methods: A Pilot Study. Prosthesis 2022;4:151–9. https://doi.org/10.3390/prosthesis4020015.
[12] S M, J H, Chf H, Ds T. Production time, effectiveness and costs of additive and subtractive computer-aided manufacturing (CAM) of implant prostheses: A systematic review. Clinical Oral Implants Research 2021;32 Suppl 21. https://doi.org/10.1111/clr.13801.
[13] Goodacre CJ, Goodacre BJ, Baba NZ. Should Digital Complete Dentures Be Part of A Contemporary Prosthodontic Education? J Prosthodont 2021;30:163–9. https://doi.org/10.1111/jopr.13289.
[14] Baldi A, Comba A, Michelotto Tempesta R, Carossa M, Pereira GKR, Valandro LF, et al. External Marginal Gap Variation and Residual Fracture Resistance of Composite and Lithium-Silicate CAD/CAM Overlays after Cyclic Fatigue over Endodontically-Treated Molars. Polymers 2021;13:3002. https://doi.org/10.3390/polym13173002.
[15] Dawood A, Marti Marti B, Sauret-Jackson V, Darwood A. 3D printing in dentistry. Br Dent J 2015;219:521–9. https://doi.org/10.1038/sj.bdj.2015.914.
[16] Piedra-Cascón W, Krishnamurthy VR, Att W, Revilla-León M. 3D printing parameters, supporting structures, slicing, and post-processing procedures of vat-polymerization additive manufacturing technologies: A narrative review. J Dent 2021;109:103630. https://doi.org/10.1016/j.jdent.2021.103630.
[17] Liu Q, Leu MC, Schmitt SM. Rapid prototyping in dentistry: technology and application. Int J Adv Manuf Technol 2006;29:317–35. https://doi.org/10.1007/s00170-005-2523-2.
[18] Allahkarami M, Hanan JC. Mapping the tetragonal to monoclinic phase transformation in zirconia core dental crowns. Dent Mater 2011;27:1279–84. https://doi.org/10.1016/j.dental.2011.09.004.
[19] McGarry TJ, Jacobson TE. The professions of dentistry and dental laboratory technology: improving the interface. J Am Dent Assoc 2004;135:220–6. https://doi.org/10.14219/jada.archive.2004.0156.
[20] Fabrizio Molinelli, Manca Enrico. La comunicazione del team protesico nell’era digitale. Dental Cadmos n.d.;5:368–74.
[21] Manifattura Artigiana, il significato autentico. Officina de Tornabuoni Firenze n.d. https://odtskincare.com/it/blog/lifestyle/manifattura-artigiana-il-significato-autentico (accessed March 18, 2023).
[22] Giorgianni F. La funzione tecnica e il mestiere dell’artigiano nella Grecia antica tra merito e responsabilità. Una rassegna critica n.d.
Do you want more information on Zhermack Dental products and solutions?
Contact us