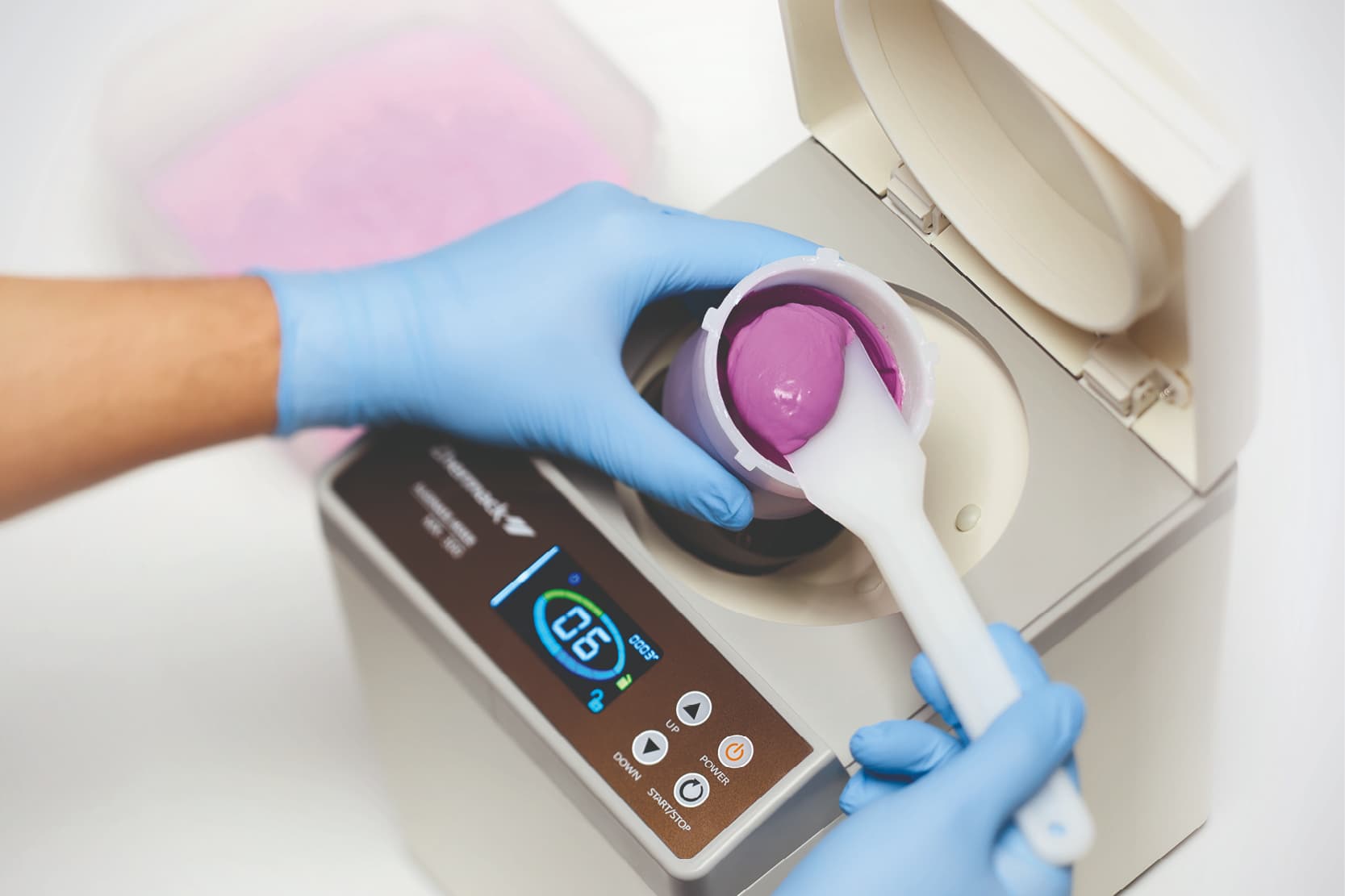
Alginate is the most commonly-used impression material in dental practices [1]. Its uses range from the fabrication of study and antagonist models to the fabrication of work models for orthodontics [2].
Alginate, which has been developed since the 1930s, is a material belonging to the irreversible hydrocolloid category. Its main advantages are its low cost, ease of use, hydrophilia, mucostaticity and patient-friendliness, thanks to its neutral scent and flavour [3,4].
On the other hand, its disadvantages include low tear resistance, poor dimensional stability, low rigidity and also the possibility of entrapping air during manual mixing.
These characteristics prevent alginate from being classified as a final impression material for fixed restorations on natural teeth and implants. However, alginate can nevertheless affect the adaptation of oral restorations as it can be used also for antagonist arches with final prosthesis.
Consequently, the way in which alginates are used is important.
Alginate mixing techniques
Alginates can be mixed using three different mixing techniques: manual, semi-automatic and automatic [5].
Manual Mixing
Manual mixing consists of measuring out the powder and water, adding the latter to the powder in a bowl, and manual mixing using a spatula.
Spatula mixing must initially aim to incorporate all the water in the powder, and must subsequently be fast and vigorous, in order to obtain a material with a creamy consistency that can provide an accurate impression of the dental arches.
However, there is no definitive guidance on how this mixing should be carried out. Although some authors recommend fast “figure-of-eight” movements [4], there is no scientific evidence to suggest that other manual mixing techniques are not able to give better results.
Semi-automatic mixing
Another technique is semi-automatic mixing. This type of mixing also requires appropriate measuring of the amounts of powder and liquid, as indicated by the manufacturer, adding the water to the powder, and initial mixing by spatula to incorporate all the water in the powder, followed by use of mechanical mixing which makes the mixing bowl turn.
In this way, the spatula is used to press the material against the inside walls of the mixing bowl to allow the most homogeneous mixing of the material possible, while reducing the air entrapped in the mix.
Although this mixing technique reduces inter-operator mixing variability, air bubbles are nevertheless incorporated into the mass of material, despite all efforts to minimise it [6].
Automatic mixing
Automatic mixing is the most recent evolution for alginate mixing.
It involves placing the previously measured out powder and water in a container that is then hermetically sealed and placed in a mixing machine that centrifuges it. Once the mixing has finished, the material is ready to be placed in an impression tray using a spatula.
This last technique has considerable advantages. Firstly, it reduces the materials’ working time leaving the operator more time for managing the subsequent steps of placing the alginate in the impression tray and taking the impression [5].
Then there are advantages regarding the mechanical characteristics. Automatic mixing has been proven to improve the accuracy of the material [7], its elastic recovery and tear resistance [8], dimensional stability [9] and compressive strength, [10] while reducing not only the air bubbles, but also the material’s internal porosity [10], almost completely eliminating it, and therefore allowing the material to behave, from a chemical and mechanical perspective, in a uniform manner.
Further advantages of high speed automatic mixing
When analysed using microtomographic and visual techniques, manually-mixed alginate has a great many air bubbles in its internal structure, unlike automatically-mixed alginate, which has almost none [5,10].
Indeed, with high-speed automatic mixing, air bubbles are removed as a result of the difference in density between the alginate particles and the air [5]. Furthermore, during this process, the temperature of the material increases slightly due to the mechanical friction between the particles of material or between the material and the mixing vessel, thereby ensuring a more even distribution also of the water molecules [5,8].
This is associated with a slight decrease in the viscosity of the alginate, which will be more fluid but nevertheless stiff before it is introduced into the patient’s mouth, thus allowing an optimum recording of the finer details [5]. Therefore, the gypsum models produced from automatically mixed alginate will have a higher surface quality and will also be more dimensionally accurate, since the expansion of the gypsum during setting is more effectively counteracted by alginate with appropriate and uniform mechanical properties throughout [10].
The importance of the mechanical characteristics of alginates
Mechanical properties, such as elastic recovery and tear resistance, are extremely important in clinical practice.
When taking impressions on patients with prostheses or orthodontic appliances it is important that the alginate does not tear in undercut areas when the impression is removed from the patient’s mouth. The material must therefore be sufficiently resistant to be removed from the mouth without tearing or deforming, but also strong enough to remain attached to the impression tray [8].
Undoubtedly, certain adhesives and/or certain shapes of impression tray can improve the alginate’s adhesion to it. However, the material’s mechanical characteristics are undeniably more important and decisive for achieving the final result [11].
Conclusions
In conclusion, we can therefore say that alginate mixing techniques can influence the chemical and physical properties of the material. Automatic mixing is generally associated with better alginate performance during both clinical and laboratory stages.
In this regard, Zhermack suggests MX-300, an automatic mixer for alginates that significantly improves the quality of the mix compared to manual mixing and helps to standardise the process.
As a matter of fact, automatic mixing using the MX-300 makes it possible to obtain reliable results regardless of the person who does the mixing.
Featuring a modern and compact design with a limited presence of undercuts to facilitate cleaning operations, it has been tested with all Zhermack alginates. The MX-300 brings out the best technical properties in any alginate, whilst avoiding potential errors caused by manual mixing.
References
[1] Morrow RM, Brown CE, Stansbury BE, deLorimier JA, Powell JM, Rudd KD. Compatibility of alginate impression materials and dental stones. J Prosthet Dent 1971;25:556–66. https://doi.org/10.1016/0022-3913(71)90214-9.
[2] Cervino G, Fiorillo L, Herford AS, Laino L, Troiano G, Amoroso G, et al. Alginate Materials and Dental Impression Technique: A Current State of the Art and Application to Dental Practice. Mar Drugs 2018;17. https://doi.org/10.3390/md17010018.
[3] Nandini VV, Venkatesh KV, Nair KC. Alginate impressions: A practical perspective. J Conserv Dent JCD 2008;11:37–41. https://doi.org/10.4103/0972-0707.43416.
[4] Dilip A, Gupta R, Geiger Z. Dental Alginate Impressions. StatPearls, Treasure Island (FL): StatPearls Publishing; 2021.
[5] Inoue K, Song YX, Kamiunten O, Oku J, Terao T, Fujii K. Effect of mixing method on rheological properties of alginate impression materials. J Oral Rehabil 2002;29:615–9. https://doi.org/10.1046/j.1365-2842.2002.00726.x.
[6] Frey G, Lu H, Powers J. Effect of mixing methods on mechanical properties of alginate impression materials. J Prosthodont Off J Am Coll Prosthodont 2005;14:221–5. https://doi.org/10.1111/j.1532-849X.2005.00047.x.
[7] Effect of mixing methods and disinfection on dimensional… – Google Scholar n.d. https://scholar.google.it/scholar?hl=it&as_sdt=0%2C5&q=Effect+of+mixing+methods+and+disinfection+on+dimensional+accuracy+of+alginate+impressio&btnG= (accessed December 5, 2022).
[8] Dreesen K, Kellens A, Wevers M, Thilakarathne PJ, Willems G. The influence of mixing methods and disinfectant on the physical properties of alginate impression materials. Eur J Orthod 2013;35:381–7. https://doi.org/10.1093/ejo/cjs031.
[9] Culhaoglu AK, Zaimoglu A, Dogan E, Ozkir SE. The influence of different mixing methods on the dimensional stability and surface detail reproduction of two different brands of irreversible hydrocolloids. Eur J Gen Dent 2014;3:17–21. https://doi.org/10.4103/2278-9626.126204.
[10] Hamilton MJ, Vandewalle KS, Roberts HW, Hamilton GJ, Lien W. Microtomographic Porosity Determination in Alginate Mixed with Various Methods. J Prosthodont 2010;19:478–81. https://doi.org/10.1111/j.1532-849X.2010.00599.x.
[11] Leung KCM, Chow TW, Woo CW, Clark RKF. Tensile, shear and cleavage bond strengths of alginate adhesive1This paper is based on a dissertation for partial fulfilment of the degree of Master of Dental Surgery of the University of Hong Kong and was presented at the 43rd Annual Conference of the British Society for the Study of Prosthetic Dentistry, Belfast, April 1996. The presentation was awarded the Schottlanders’ Poster Prize.1. J Dent 1998;26:617–22. https://doi.org/10.1016/S0300-5712(97)00045-6.
Do you want more information on Zhermack Dental products and solutions?
Contact us