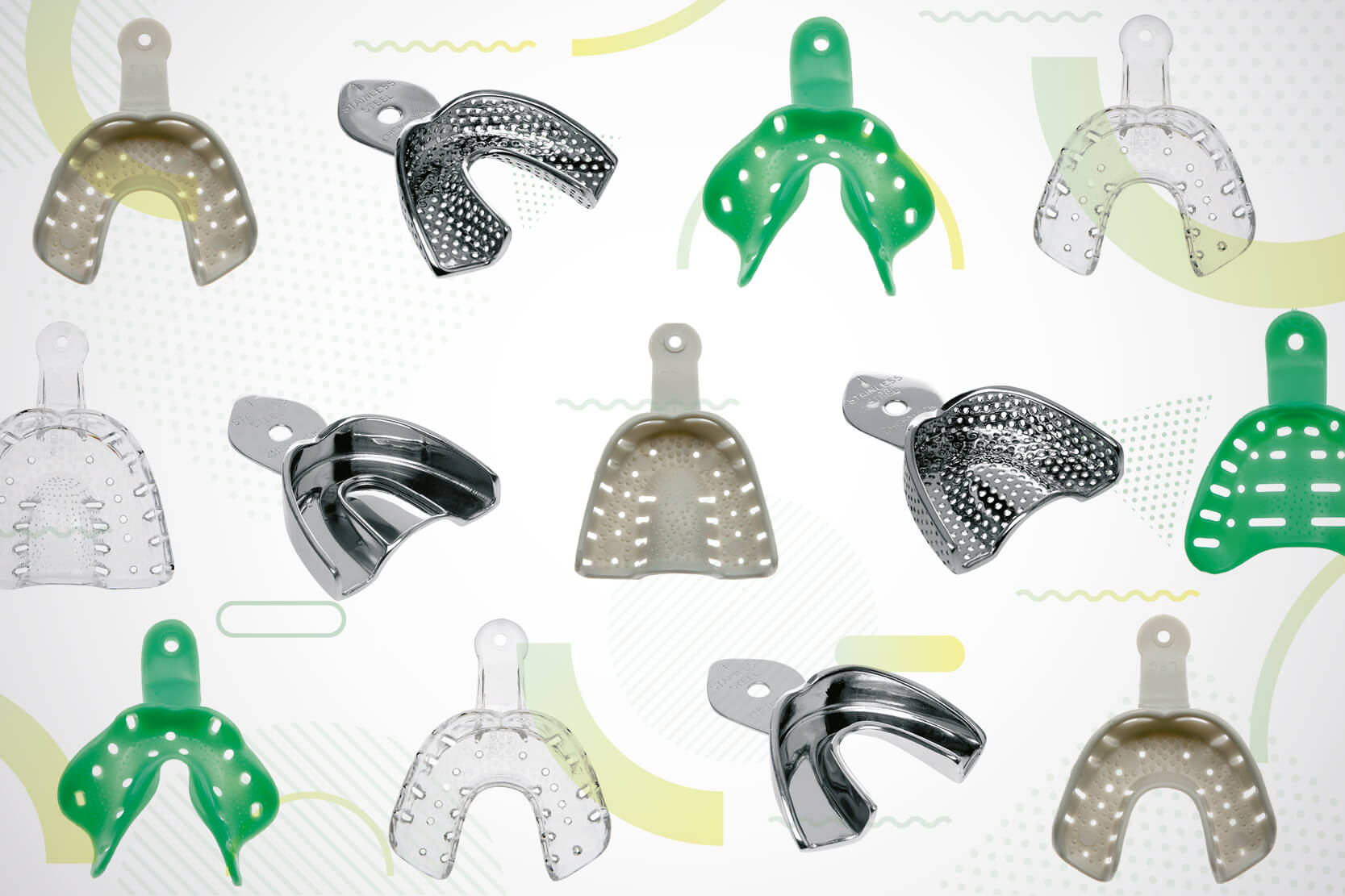
Impression trays are devices used to carry, contain and control impression material during the taking of an impression. They also serve as containers for holding impression material during the production of a negative copy. (1)
In short, impression trays permit the application of impression material whenever needed, along with the production of negative copies.
All impression trays share certain common features: a handle, a floor and flanges.
Given that impression materials and the features they reproduce vary so much, it is logical that the devices used to carry, contain and control those materials during impression taking will vary too.
Impression trays come in standard form and as custom impression trays.
Custom impression trays
Custom impression trays are individually made, i.e. are produced specifically for an individual patient. Having an impression tray that accurately reflects the anatomy of the patient’s arch is a great advantage as the material used to take the impression will be distributed more accurately and more evenly over the relevant areas.
Impression trays can be produced using conventional, stone model based techniques (2) or using digital techniques (3). Compared to standard, stock impression trays, custom versions offer the advantage of allowing a controlled and constant thickness to be achieved in the impression material. (4)
Custom impression trays produced using conventional methods are normally made from resin (5), while those produced using digital CAD/CAM software are typically made from PLA (polyactide) by means of 3D printing (6). Conventional techniques are still the most commonly used today: a coating of resin is applied to a spaced stone model, the excess is removed, the handle formed and the tray is cured.
Custom impression trays do not provide any mechanical retention for the impression material, unless holes have been made in them with a bur. Before the impression can be taken, therefore, a film of adhesive specially formulated for use with impression material must be applied.
Impression trays can easily be flanged for use with edentulous patients or drilled at the location of implant transfers for use in “open tray” procedures.
Standard impression trays
Standard impression trays, on the other hand, are ready made, i.e. based on standard arch measurements and shapes. There are various types of standard impression tray on the market. Let us take a look at the main differences between them.
The first factor determining variation in impression trays is the anatomy of the individual patient, which can vary significantly. Anatomical differences play a fundamental role in the choice of impression tray, which may need to be larger or smaller depending on the patient from whom the impression is to be taken. There are various ways to determine the correct size for an impression tray: you can try one out directly in the patient’s oral cavity or you can use a special compass to determine the diameter of the arch intraorally and then select the most suitable size of tray.
Standard impression trays come in 6 sizes numbered from 1 to 6, starting with the smallest diameter and progressing to the largest. Alternatively trays (and especially plastic trays) may be marked with sizes xs, s, m, l and xl.
Some impression trays cover the entire arch of the patient while others cover only a semi-arch (quadrant). Still others, referred to as sectional trays, cover only a specific section of the arch such as, for example, the anterior group (second and fifth sextant).
Standard impression trays can be made from metal or plastic.
Metal impression trays
Metal impression trays are more rigid and therefore offer greater accuracy and precision than flexible plastic alternatives. (7) Rigid impression trays are to be preferred whenever a good degree of accuracy is required, as they do not flex during positioning or during removal of the impression.
Metal impression trays can be perforated or non-perforated and come with or without rim locks.
When removed from the oral cavity, perforated trays with rim locks offer excellent mechanical retention for the impression material which is therefore unlikely to become detached from the tray or distort. Because the material tends to come out from the holes, however, the same pressure (vis a tergo) applied using a non-perforated tray may not be achieved.
Impression trays with no form of mechanical retention (holes or rim locks) need to be coated with a special adhesive to retain the impression material (8). In the absence of mechanical retention, chemical adhesion between the tray and the impression material is essential.
“Schreinemaker” trays (9) are special metal impression trays intended for use with edentulous patients. These trays come in various upper and lower sizes and in different arch shapes. Schreinemaker impression trays are shaped and flanged to suit the specific anatomies of edentulous patients. The choice of correct tray size must be determined intraorally using a special compass.
Standard plastic impression trays
Standard plastic impression trays come in various types. The best are those in rigid plastic (7). These trays may be perforated or non-perforated and offer more or less mechanical retention. The main benefit of plastic impression trays is the ease with which holes can be made in them. This is frequently required in “open tray” procedures which need a hole at implant transfers to unscrew the transfers through the impression tray. (10)
Plastic impression trays are generally single use (disposable).
Another special type of plastic impression tray is the “dual-arch” tray. Dual-arch trays consist of a handle, an external structure (vestibular and lingual) in rigid plastic in the shape of a “U” and a floor made from flexible plastic mesh. To use this type of tray, impression material is applied to both sides of the flexible mesh and the impression is taken by closing the patient’s mouth to maximum intercuspidation. This technique can be used to register the arch of interest (on which the preparation is being made), the antagonist arch and the intermaxillary occlusion in a single step (11).
The dual-arch technique of impression taking, however, also has some significant limitations: it can only be used successfully with impressions involving one or at the most two preparations in the same quadrant, and stable occlusal contact must be maintained at maximum intercuspidation. (12)
Zhermack solution for impression trays
The world of impression trays is extremely vast and many alternative products are to be found on the market. It is therefore up to the dental practice to evaluate each individual case and to choose the best impression tray to suit the procedure in question.
Universal Tray Adhesive is Zhermack’s solution to the problem of limited mechanical retention in non-perforated resin or metal trays. Universal Tray Adhesive ensures adhesion between polyvinylsiloxanes (addition silicones) and custom resin impression trays or non-perforated metal impression trays, and prevents impression material from separating from the tray. Rapid solvent evaporation is one of this product’s key features.
Bibliography
(1) Ferro, K. J., Morgano, S. M., Driscoll, C. F., Freilich, M. A., Guckes, A. D., Knoernschild, K. L., … & Twain, M. (2017). The glossary of prosthodontic terms.
(2) Terry, D. A., Tric, O., Blatz, M., & Burgess, J. O. (2010). The custom impression tray: fabrication and utilization. Dent Today, 29, 132-134.
(3) Kanazawa, M., Iwaki, M., Arakida, T., & Minakuchi, S. (2018). Digital impression and jaw relation record for the fabrication of CAD/CAM custom tray. journal of prosthodontic research, 62(4), 509-513.
(4) Bomberg, T. J., Hatch, R. A., & Hoffman Jr, W. (1985). Impression material thickness in stock and custom trays. The Journal of prosthetic dentistry, 54(2), 170-172.
(5) Breeding, L. C., Dixon, D. L., & Moseley, J. P. (1994). Custom impression trays: Part I—Mechanical properties. The Journal of prosthetic dentistry, 71(1), 31-34.
(6) Chen, H., Yang, X., Chen, L., Wang, Y., & Sun, Y. (2016). Application of FDM three-dimensional printing technology in the digital manufacture of custom edentulous mandible trays. Scientific reports, 6(1), 1-6.
(7) Carrotte, P. V., Johnson, A., & Winstanley, R. B. (1998). The influence of the impression tray on the accuracy of impressions for crown and bridge work–an investigation and review. British dental journal, 185(11), 580-585.
(8) Marafie, Y., Looney, S., Nelson, S., Chan, D., Browning, W., & Rueggeberg, F. (2008). Retention strength of impression materials to a tray material using different adhesive methods: An in vitro study. The Journal of prosthetic dentistry, 100(6), 432-440.
(9) Beale, T. O. N. Y. (2007). The essential elements of impression tray design. International Dentistry South Africa, 9(4), 58-60.
(10) Burns, J., Palmer, R., Howe, L., & Wilson, R. (2003). Accuracy of open tray implant impressions: an in vitro comparison of stock versus custom trays. The Journal of prosthetic dentistry, 89(3), 250-255.
(11) Cayouette, M. J., Burgess, J. O., Jones Jr, R. E., & Yuan, C. H. (2003). Three-dimensional analysis of dual-arch impression trays. Quintessence international, 34(3).
(12) Small, B. W. (2012). Revisiting impressions using dual-arch trays. General dentistry, 60(5), 379-381.
Do you want more information on Zhermack Dental products and solutions?
Contact Us